Behaviour Analysis of Induction Motor Under Various Fault Conditions of Rotor bar at Different Loading
Kalpana Sheokand1 , Neelam Turk2
- Department of Electronics Engineering, YMCA University of Science and Technology, Faridabad, India.
- Department of Electronics Engineering, YMCA University of Science and Technology, Faridabad, India.
Correspondence should be addressed to: kshehrawat@gmail.com.
Section:Research Paper, Product Type: Journal Paper
Volume-6 ,
Issue-2 , Page no. 18-24, Feb-2018
CrossRef-DOI: https://doi.org/10.26438/ijcse/v6i2.1824
Online published on Feb 28, 2018
Copyright © Kalpana Sheokand, Neelam Turk . This is an open access article distributed under the Creative Commons Attribution License, which permits unrestricted use, distribution, and reproduction in any medium, provided the original work is properly cited.
View this paper at Google Scholar | DPI Digital Library
How to Cite this Paper
- IEEE Citation
- MLA Citation
- APA Citation
- BibTex Citation
- RIS Citation
IEEE Citation
IEEE Style Citation: Kalpana Sheokand, Neelam Turk, “Behaviour Analysis of Induction Motor Under Various Fault Conditions of Rotor bar at Different Loading,” International Journal of Computer Sciences and Engineering, Vol.6, Issue.2, pp.18-24, 2018.
MLA Citation
MLA Style Citation: Kalpana Sheokand, Neelam Turk "Behaviour Analysis of Induction Motor Under Various Fault Conditions of Rotor bar at Different Loading." International Journal of Computer Sciences and Engineering 6.2 (2018): 18-24.
APA Citation
APA Style Citation: Kalpana Sheokand, Neelam Turk, (2018). Behaviour Analysis of Induction Motor Under Various Fault Conditions of Rotor bar at Different Loading. International Journal of Computer Sciences and Engineering, 6(2), 18-24.
BibTex Citation
BibTex Style Citation:
@article{Sheokand_2018,
author = {Kalpana Sheokand, Neelam Turk},
title = {Behaviour Analysis of Induction Motor Under Various Fault Conditions of Rotor bar at Different Loading},
journal = {International Journal of Computer Sciences and Engineering},
issue_date = {2 2018},
volume = {6},
Issue = {2},
month = {2},
year = {2018},
issn = {2347-2693},
pages = {18-24},
url = {https://www.ijcseonline.org/full_paper_view.php?paper_id=1697},
doi = {https://doi.org/10.26438/ijcse/v6i2.1824}
publisher = {IJCSE, Indore, INDIA},
}
RIS Citation
RIS Style Citation:
TY - JOUR
DO = {https://doi.org/10.26438/ijcse/v6i2.1824}
UR - https://www.ijcseonline.org/full_paper_view.php?paper_id=1697
TI - Behaviour Analysis of Induction Motor Under Various Fault Conditions of Rotor bar at Different Loading
T2 - International Journal of Computer Sciences and Engineering
AU - Kalpana Sheokand, Neelam Turk
PY - 2018
DA - 2018/02/28
PB - IJCSE, Indore, INDIA
SP - 18-24
IS - 2
VL - 6
SN - 2347-2693
ER -
![]() |
![]() |
![]() |
1783 | 1097 downloads | 544 downloads |
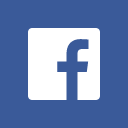
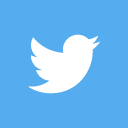
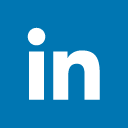
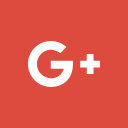
Abstract
Induction motors have a vital influence in the protected and productive running of any modern plant. Faulty condition of these motors because of electrical and mechanical faults may antagonistically affect on line production and can cause unforeseen downtime. Along these lines, discovery of variations from the norm in the motor would maintain a strategic distance from exorbitant breakdowns and especially early location of early rotor bar faults are critical for productive activity of substantial induction motors. In this paper, execution of induction motor under 2D different failure’s modes like broken rotor bars are examined under different loading condition using FEM approach. Maxwell 2D Transient solver is utilized for breaking down the conductor of motor under solid and diverse faulty conditions.
Key-Words / Index Term
Maxwell Equations, Eddy Effect, Fault Detection, Broken rotor bar fault
References
[1] A. H. Bonnet, “Analysis of rotor failures in squirrel cage induction machines,” IEEE Trans. Ind. Appl., vol. 24, no. 6, pp. 1124–1130,
Nov./Dec. 1988.
[2] A. H. Bonnet and G. C. Soukup, “Cause and analysis of stator and rotor failures in three-phase squirrel-cage induction motors,” IEEE Trans. Ind. Appl., vol. 28, no. 4, pp. 921–937, Jul./Aug. 1992.
[3] M. L. Sin, W.L.Soong and N.Ertugrul, "Induction Machine On-Line Condition Monitoring and Fault Diagnosis - A Survey", AUPEC2003, Australasian Universities Power Engineering Conference, Christchurch, New Zealand, pp. 1-6, 2003.
[4] W.R. Finley, M.M. Hodowanec and W.G. Holter, “An Analytical Approach to Solving Motor Vibration Problems,” IEEE Trans. on Ind. Appl., vol. 36, no. 5, Sep./Oct. 2000, pp.1467-1480.
[5] N. Arthur and J. Penman, “Induction Machine Condition Monitoring with Higher Order Spectra,” IEEE Trans. on Ind. Electronics, vol. 47, no. 5, Oct. 2000, pp. 1031- 1041.
[6] B.S. Payne, A. Ball and F. Gu, “Detection and Diagnosis on Induction Motor Faults using Statistical Measures,” International Journal of Condition Monitoring and Diagnostics Engineering Management, vol. 5, no. 2, Apr. 2002, pp. 5-19.
[7] M.F. Cabanas, M.G. Melero, G.A. Orcajo, F. Rodriguez Faya and J. Solares Sariego, “Experimental Application of Axial Leakage Flux to the Detection of RotorAsymmetries, Mechanical Anomalies and Interturn Short-Circuits in Working Induction Motors,” Int. Conf. on Elect. Machines, 1998, pp.420-425.
[8] Sergio CRUZ, Flavio GASPAR, “A new method to diagnose rotor faults in 3- phase induction motors coupled to time varying loads,” PRZEGLAD ELEKTROTECHNICZNY (Electrical Review), ISSN 0033-2097, R.88 NR 1a/ 2012, pp. 202-206
[9] Manuel Pineda- Sanchez, Martin Riera-Guasp, Jose Alfonso Antonino-Daviu, Jose Roger-Folch, Juan Perez- Cruz and Ruben Puche-Panadero, “Instantaneous frequency of the left sideband harmonic during the start –up transient: A new method for diagnosis of broken bars,” IEEE Trans. on Industrial Electronics, Vol.56, No. 11, Nov 2009, pp. 4557-4570.
[10]Ahmed, N. Ertugrul, and W. L. Soong, "A Study on the Detection of Fault Frequencies for Condition Monitoring of Induction Machines,” Australian Universities Power Engineering Conference, Tasmania, Australia 2005.
[11] R. Fiser and S. Ferkolj, “Application of Finite Element Method to Predict Damaged Induction Motor Performance,” IEEE Trans. on Magnetics, Vol. 37, no 5,Sep. 2001, pp. 3635-3639.
[12] W. T. Thomson and A. Barbour, “On-Line Current Monitoring and Application of a Finite Element Modelling of Induction Motor Faults with Finite Element Method to predict the Level of Static Airgap Eccentricity in Three-Phase Induction Motors,” IEEE Transactions on energy Conversion, Vol. 13, no 4, December 1998, pp. 347-352.
[13] R. J. Tallam, T. G. Habetler and R. G. Harley, “Transient Model for Induction Machines With Stator Winding Turns Faults,” IEEE Transactions on I8ndustry Applications, Vol. 38, no 3, May/June 2002, pp. 632-637.
[14] E. Schaeffer, E. L. Carpentier and M. E. Zaim, “Failure Detection in Induction Machine by Means of Parametric Identification,” CESA’98, IEEE Conference on Computational Engineering in Systems Applications, Nabeul-Hammament, Tunisia, 1-4 April 1998.
[15] R. Beguenane and M.E.H. Benbouzid, “Induction Motors Thermal Monitoring By Means of Rotor-Resistance Identification”, IEEE Transaction on Energy Conversion, Vol. 14, No 3, September 1999, pp 566 – 570.
[16] J. F. Bangura and N. A. Demerdash, “Diagnosis and Charactization of effects of Broken Rotor Bars and Connectors in Squirrel-Cage Induction Motors by a Time-Stepping Coupled Finite Element-State Space Modeling Approach,” IEEE Transactions on energy Conversion, Vol. 15, December 1999, pp. 1167-1176.
[17] R. J. Povinelli, J. F. Bangura, N. A. Demerdash and R. H. Brown, “Diagnostic of Bar and End-Ring Connector Breakage Faults in Poly-phase Induction Motors Through a Novel Dual Track of Time-Stepping Coupled FE-State Space Modelling,” IEEE Transactions on energy Conversion, Vol. 17, no 1, March 2002, pp. 39-46.
[18] F. Filippetti, G. Franceschini, P. Vas and C. Tassoni “Broken Bar Detection in Induction Machines: Comparison between Current spectrum Approach and Parameter Estimation Approach”, IEEE Industry Application Society, Vol. 1, pp. 95-102, 1994.
[19] F. Filippetti, G. Franceschini and C. Tassoni “Neural Networks Aided On-Line Diagnostics of Induction Motor Rotor Faults”, IEEE Industry Application Society, Vol. 1, pp. 316-323, 1993.
[20] M.L. Sin, W.L. Soong and N. Ertugrul, "Induction Machine On-Line Condition monitoring and Fault diagnosis- A Survey" AUPEC 2003, Christchurch, New Zealand.
[21] F. Filippetti, G. Franceschini, C. Tassoni, G. Gentile, S. Meo, A. Ometto and N.Rotondale, “Deterministic Approach and Neural Network Approach for Stator Short Circuits Diagnosis in Induction Motor,” 7 Industry Application Society, Vol. 1, pp. 316-323, 1993.
[22] M. Y. Chow, “Methodologies of Using Neural Network and Fuzzy Logic Technologies for Motor Incipient Fault Detection,” World Scientific, Singapore,1997.
[23] W. T. Thomson and M. Fenger, “Current Signature Analysis to Detect Induction Motor Faults”, IEEE Industry Applications Magazine, pp. 26-34, July/August 2001.
[24] Ahmed, R. Supangat, J. Grieger, J, N. Ertugrul, and W.L Soong, "A Baseline Study for On-Line Condition Monitoring of Induction Machines." Australian Universities Power Engineering Conference, Brisbane, Australia 2004,
[25] M.L. Sin, W.L. Soong and N. Ertugrul, "Induction Machine On-Line Condition monitoring and Fault diagnosis- A Survey" AUPEC 2003, Christchurch, New Zealand.
[26] A.A. Da Silva et al., “Rotating machinery monitoring and diagnosis using short-time Fourier transform and wavelet techniques,” in Proc. 1997 Int. Conf. Maintenance and Reliability, vol. 1, Knoxville, TN, pp. 14.01–14.15.
[27] B. S. Payne, A. Ball and F. Gu, “Detection and Diagnosis on Induction Motor Faults using Statistical Measures”, International Journal of Condition Monitoring and Diagnosis Engineering Management, vol. 5, no.2, April 2002, pp.5-19.
[28] A. H. Bonnett and G. C. Soukup, “Analysis of Rotor Failures in Squirrel-Cage Induction Motors,” IEEE Transactions on Industry Applications, vol. 24, no. 6, pp. 1124–1130, November/December 1988