MODELING AND REVIEW ON ELECTROCHEMICAL DISCHARGE MACHINING
Sandeep Kumar Pandey1 , Dilip Gehlot2 , Surbhi Singh3 , Lokesh Kharadi4
Section:Review Paper, Product Type: Journal Paper
Volume-05 ,
Issue-02 , Page no. 103-109, Dec-2017
CrossRef-DOI: https://doi.org/10.26438/ijcse/v5si2.103109
Online published on Dec 31, 2017
Copyright © Sandeep Kumar Pandey, Dilip Gehlot, Surbhi Singh, Lokesh Kharadi . This is an open access article distributed under the Creative Commons Attribution License, which permits unrestricted use, distribution, and reproduction in any medium, provided the original work is properly cited.
View this paper at Google Scholar | DPI Digital Library
How to Cite this Paper
- IEEE Citation
- MLA Citation
- APA Citation
- BibTex Citation
- RIS Citation
IEEE Citation
IEEE Style Citation: Sandeep Kumar Pandey, Dilip Gehlot, Surbhi Singh, Lokesh Kharadi, “MODELING AND REVIEW ON ELECTROCHEMICAL DISCHARGE MACHINING,” International Journal of Computer Sciences and Engineering, Vol.05, Issue.02, pp.103-109, 2017.
MLA Citation
MLA Style Citation: Sandeep Kumar Pandey, Dilip Gehlot, Surbhi Singh, Lokesh Kharadi "MODELING AND REVIEW ON ELECTROCHEMICAL DISCHARGE MACHINING." International Journal of Computer Sciences and Engineering 05.02 (2017): 103-109.
APA Citation
APA Style Citation: Sandeep Kumar Pandey, Dilip Gehlot, Surbhi Singh, Lokesh Kharadi, (2017). MODELING AND REVIEW ON ELECTROCHEMICAL DISCHARGE MACHINING. International Journal of Computer Sciences and Engineering, 05(02), 103-109.
BibTex Citation
BibTex Style Citation:
@article{Pandey_2017,
author = {Sandeep Kumar Pandey, Dilip Gehlot, Surbhi Singh, Lokesh Kharadi},
title = {MODELING AND REVIEW ON ELECTROCHEMICAL DISCHARGE MACHINING},
journal = {International Journal of Computer Sciences and Engineering},
issue_date = {12 2017},
volume = {05},
Issue = {02},
month = {12},
year = {2017},
issn = {2347-2693},
pages = {103-109},
url = {https://www.ijcseonline.org/full_spl_paper_view.php?paper_id=307},
doi = {https://doi.org/10.26438/ijcse/v5i2.103109}
publisher = {IJCSE, Indore, INDIA},
}
RIS Citation
RIS Style Citation:
TY - JOUR
DO = {https://doi.org/10.26438/ijcse/v5i2.103109}
UR - https://www.ijcseonline.org/full_spl_paper_view.php?paper_id=307
TI - MODELING AND REVIEW ON ELECTROCHEMICAL DISCHARGE MACHINING
T2 - International Journal of Computer Sciences and Engineering
AU - Sandeep Kumar Pandey, Dilip Gehlot, Surbhi Singh, Lokesh Kharadi
PY - 2017
DA - 2017/12/31
PB - IJCSE, Indore, INDIA
SP - 103-109
IS - 02
VL - 05
SN - 2347-2693
ER -
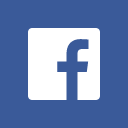
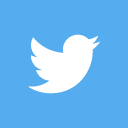
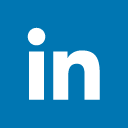
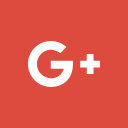
Abstract
Electrochemical discharge machining (ECDM) process utilizes the spark discharge produced by gas film formation during electrolysis. In the conventional ECDM process, precise control of the spark generation is difficult because of the randomness of gas film formation which results in the significant deterioration of process qualities such as excessive overcut, poor machining accuracy and low machining repeatability. The undesirable overcut phenomenon strictly hinders the dimensional miniaturization of CDM process especially when the diameter of the applied tool is much smaller than 100 ptm. In this study a side insulated tool and dilute electrolyte concentration is proposed to reduce the undesirable overcut and thus, to improve the machining resolution of the ECDM process. Experiments are conducted with various machining parameters, such as spark ignition voltage, electrolyte concentration, and tool insulation. As a result, the feasibility of miniaturization in the ECDM process is phenomena. successfully improved by reducing the excessive overcut
Key-Words / Index Term
ECDM,Micro fabrication,Ansys,Modeling. Micro-Electro-Mechanical systems(MEMS)
References
[1]. Basak I and Ghosh A. 1996. Mechanism of spark generation during electrochemical discharge machining: a theoretical model and experimental verification. J Mater Process Tech., 62: 46-53.
[2]. Bhattacharyya, B., Doloi, B.N. and Sorkhel, S.K. 1999. Experimental investigations into electrochemical discharge machining (ECDM) of non-conductive ceramic materials. J Mater Process Tech., 95: 145-154.
[3]. Bhattacharyya, B., Doloi, B.N. and Sorkhel, S.K. 1999.Experimental investigations into electrochemical discharge machining (ECDM) of non-conductive ceramic materials. J Mater Process Tech., 95: 145-154. 4.Bhondwe, K.L. et a J.A. McGeough, W. Munro, C. White, Comparative studies of ecm, edm and ecam, Precision Engineering 39 (1981) 155–160. (62. Kurafuji H and Suda
[4]. Electrical discharge drilling of glass, CIRP Ann 1968;16: 415-419.Bhondwe,
[5]. K.L., Yadava, V. and Kathiresan, G. 2006. Finiteelement prediction of material removal rate due to electrochemical spark machining. Int J Mach Tool Manu 46:1699–1706.
[6]. Cao, X.D., Kim, B.H. and Chu, C.N. 2009. Micro structuring of glass with features less than 100 μm by electrochemical discharge machining. Precis Eng., 33: 459–465.
[7]. Cao, X.D., Kim, B.H. and Chu, C.N. 2012. Hybrid micromachining of glass using ECDM and micro grinding. Int J PrecisEng Man., 14(1): 5–10.
[8]. Cook, N.H., Foote, G.B., Jordan, P. et al. 1973. Experimental studies in electro-machining. J EngInd-T ASME 95(4): 945-950.
[9]. Doloi, B., Mitra, S., Sorkhel, S.K. 1997. Experimental analysis on the electrochemical discharge machining (ECDM) system for advanced ceramics, International Conference on Precision Engineering, ICPE, Taipei, Taiwan, pp. 715±720. Gautam,
[10]. N. and Jain, V.K. 1998. Experimental investigations into ECSD process using various tool kinematics. Int J Mach Tool Manu., 39: 15-27. Ghosh, A. 1997. Electrochemical Discharge Machining:
[11]. Jawalkar CS. Investigation on performance enhancement of ECDM process while machining glass. PhD thesis. Roorkee: Indian Institute of Technology Roorkee, 2013.
[12]. Jawalkar, C.S., Sharma, A.K. and Kumar, P. 2012.Micromachining with ECDM: research potentials andexperimental investigations. World AcadSci Eng Technol,61: 90–95.Khairy, A.B.E. and McGeough, J.A. 1989. Die-sinking by electroerosion-dissolution machining. CIRP Ann ManufTechnol, 39: 191-196.
[13]. Krӧtz, H., Roth, R. and Wegener, K. 2013. Experimental investigation and simulation of heat flux into metallic surfaces due to single discharges in micro-electrochemical arc machining (micro-ECAM). Int J AdvManufTechnol, 68: 1267–1275.
[14]. Kulkarni, A., Sharan, R. and Lal, G.K. 2003. Measurement of temperature transients in the electrochemical discharge machining process. Temperature: its measurement and control in science and industry. In: Eighth Temperature Symposium, AIP Conference Proceedings, Melville, NY, 4: 1069–1074.
[15]. Kulkarni, A., Sharan, R. and Lal, G.K. 2002. An experimental study of discharge mechanism in electrochemical discharge machining. Int J Mach Tool Manu., 42: 1121–1127.
[16]. Lijo, P. and Hiremath, S.S. 2014. Characterisation of micro channels in electrochemical discharge machining process. ApplMech Mater., 490-491: 238–242.
[17]. Liu, J.W., Yue, T.M. and Guo, Z.N. 2009. Wire electrochemical discharge machining of Al2O3 particle reinforced aluminum alloy 6061. Mater Manuf Process, 24: 446–453. McGeough, J.A. 1974. Principles of Electrochemical Machining, Chapman & Hall, New York. (3) Micromachining Using Electro Chemical Discharge Phenomenon, Rolf Wuthrich, 2nd edition.